

Why Delta?
Why outsource to delta? Experience the benefits of the delta difference:
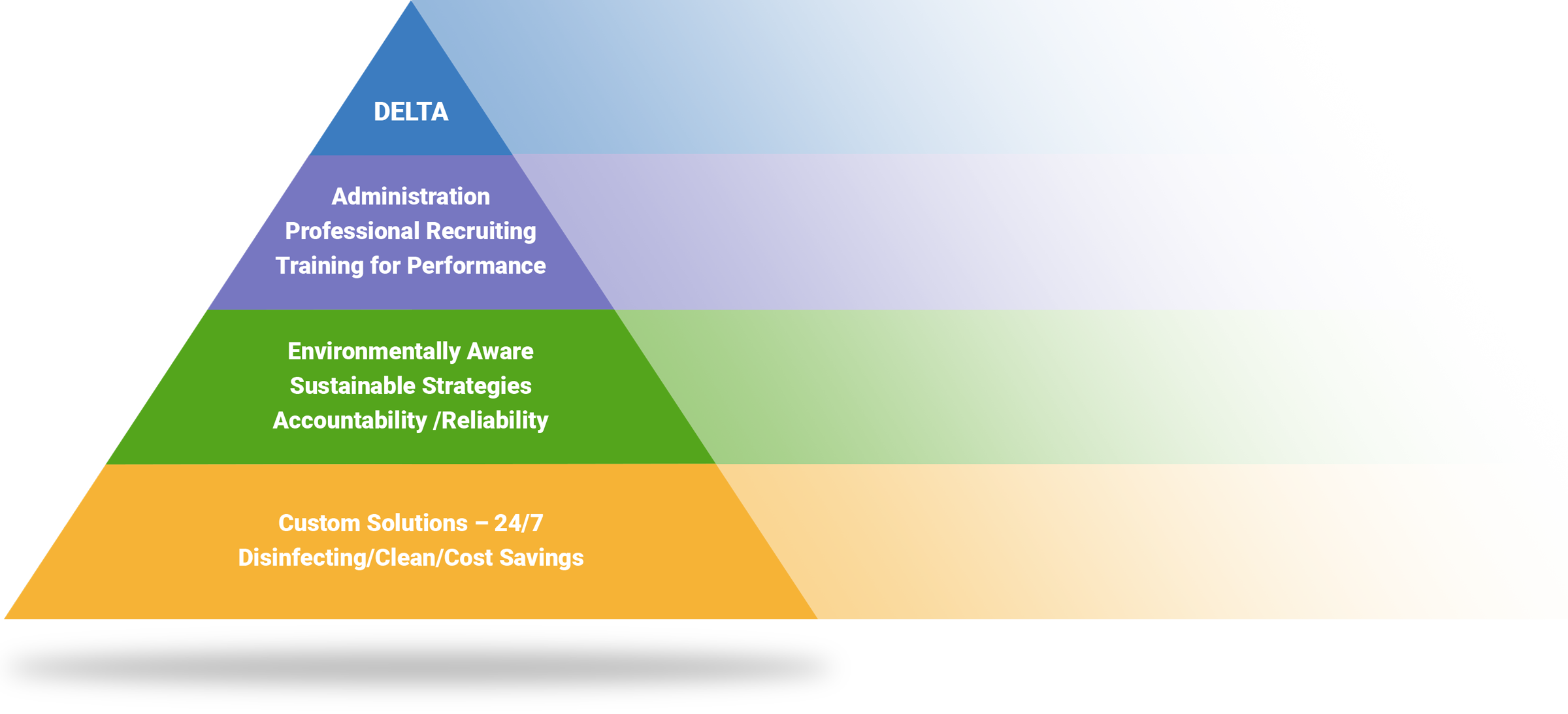

Business Continuity Plan
Delta Building Services has developed a plan to not only manage our accounts in a superior manner on a daily basis, but to continue our unparalleled service in an emergency situation. All of the business critical functions have been identified and plans have been made to preserve them if an event occurs that may threaten daily operations.
On a daily basis, a backup of all company records is updated and removed from company property, thus ensuring that all clients, insurance, financial, tax and employee record information is current and is safely stored on disk. This back up facilitates the continuance of business by providing the necessary data for all business functions and the information to renew any business licenses if an emergency occurs and access to the office is impossible. Additionally, each Executive and Manager has a database on their handheld computer with contact names, phone numbers and email addresses for every Building Manager, Site Supervisor and employee.
The Executives, Operations Manager and District Managers have set up an emergency response system with clients and employees. It includes an email alert and an 800 number voice recording. Outside of business hours, the office phones are managed by Anserve; our contracted answering service. In an emergency situation, any call will be connected to Anserve. A message is then immediately dispatched to one of the principals or the Operations Manager.
In the event of a disaster, we have established a Labor Outreach Program and have a network of hundreds of employees on retainer. They have been hired to work in instances of absenteeism or in an emergency situation. They are dispatched by our managers as needed.
We currently store two months worth of cleaning inventory in our onsite warehouse. Additionally, we store necessary supplies and equipment at each client’s location to facilitate uninterrupted service at all times. As a safety measure, we pre-purchase supplies which we store at our vendor’s warehouse. These supplies are available to us at anytime and can be retrieved if access to our warehouse is impossible.
Finally, Delta has created a coalition with neighboring businesses. This network provides support from and to nearby companies in the event of a disaster, pandemic or fire. A written plan has been created to provide services, offices space, phone banks, computer access and resources to neighboring companies if any business has been interrupted due to unforeseen circumstances.
Delta feels well prepared for any emergency situation. We have simulated drills to evaluate staff performance in such an instance and believe that our business would continue smoothly and without interruption under any circumstance.

Quality Control Management
Delta ownership and management is committed to quality service on all levels. The ideals and the mechanisms of quality service are reinforced throughout the organization, and monitored to achieve results.
Achieving customer satisfaction is the motivation behind this commitment. It is the “product” we must deliver.
Identifying and understanding the needs of the client make Delta Supervisors and District Managers essential parts of the process. The Site Supervisor responds to the customer’s needs directly by virtue of their presence in the facility every day. Supervisors and cleaning personnel are given support and guidance from pro-active management, empowering them to make their own decisions on how to get the job done to the customer’s satisfaction.
Rather than responding to directives from outside management, as is traditional in the industry, supervision is trained to take responsibility for the service process and achieving Delta’s goals within that process.
Empowerment gives the Site Supervisors the authority to make changes in systems or personnel that are necessary to achieve their objectives.
The actions of supervision are guided by their knowledge of the customer’s needs, inspection data from upper management and input from site personnel. Positive results from changes in specific areas can be applied throughout the site. Progressive or new ideas to improve quality that are tested and proven can be implemented throughout the company.
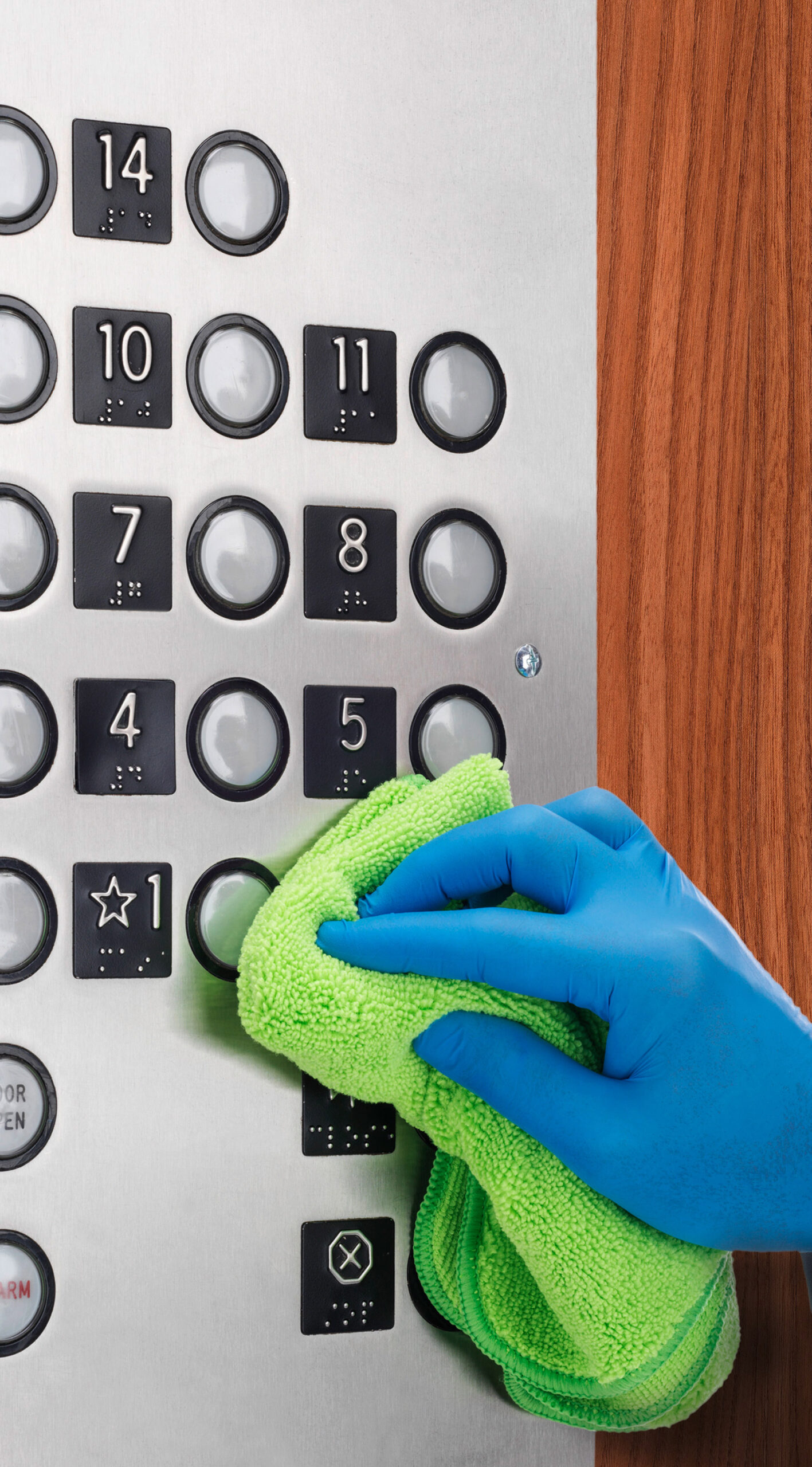

What You Can Expect
Delta will assign to your facility a Quality Control Representative who answers directly to the President, David Korn, and who operates independently of the Operations Department. This representative is concerned solely with the quality of the work and client satisfaction.
Your representative will visit your facility one time per month, to inspect and ensure that Delta is exceeding your expectations, using our inspection software, Cleantelligent, to monitor and track key performance indicators. Cleantelligent is the industry’s premier tool for Quality Control Inspections. You are welcome and encouraged to accompany your representative during these inspections so that you are aware of what Quality Control is looking for and to give your representative an opportunity to learn of any special concerns that you may have.
Both the Regional District Manager and the Director of Operations will also do weekly and bi-monthly visits. All visitation reports are given to the President, David Korn for review.

Technology
Delta has invested a tremendous amount of resources in staying ahead of the curve, when it comes to all aspects of cutting edge technology with respect to Equipment, Quality Control, Time Keeping, Payroll, Employee Retention, Supplies Ordering, Invoicing and all Client Communications.
Cleantelligent Efficiency
Cleantelligent is the industry’s premier system for scheduling and performing quality control inspections. The system allows Delta to set and track KPI’s, working closely with our client contact. Cleantelligent keeps Delta on the cutting edge of supportive technology.
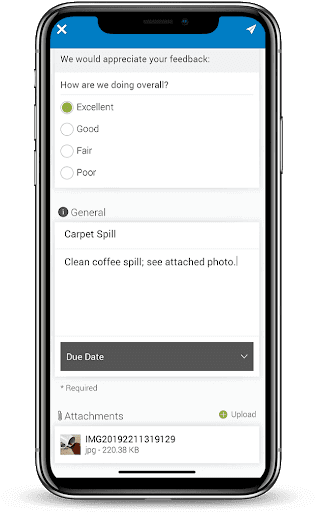
DELTA 360
Benefits
Delta 360 is a portal-based system that Delta uses internally to control budgets, approvals, payroll, and invoicing on behalf of our clients, all in one interface. The efficiency gained through this system assures our clients the highest possible level of accuracy and accountability.
How It Works
- Employees punch into a specific geo-fenced job using Delta’s time keeping system.
- Each job has a corresponding department in payroll.
- The hours punched in the system are then compared to the budget for that job.
- Approved hours are sent to ADP for payroll processing.
- Actual monies paid out are sent back to Delta 360 and subsequently checked for accuracy.
- Job tickets are checked for proper approvals and Purchase Order Numbers
- Invoices are then generated.
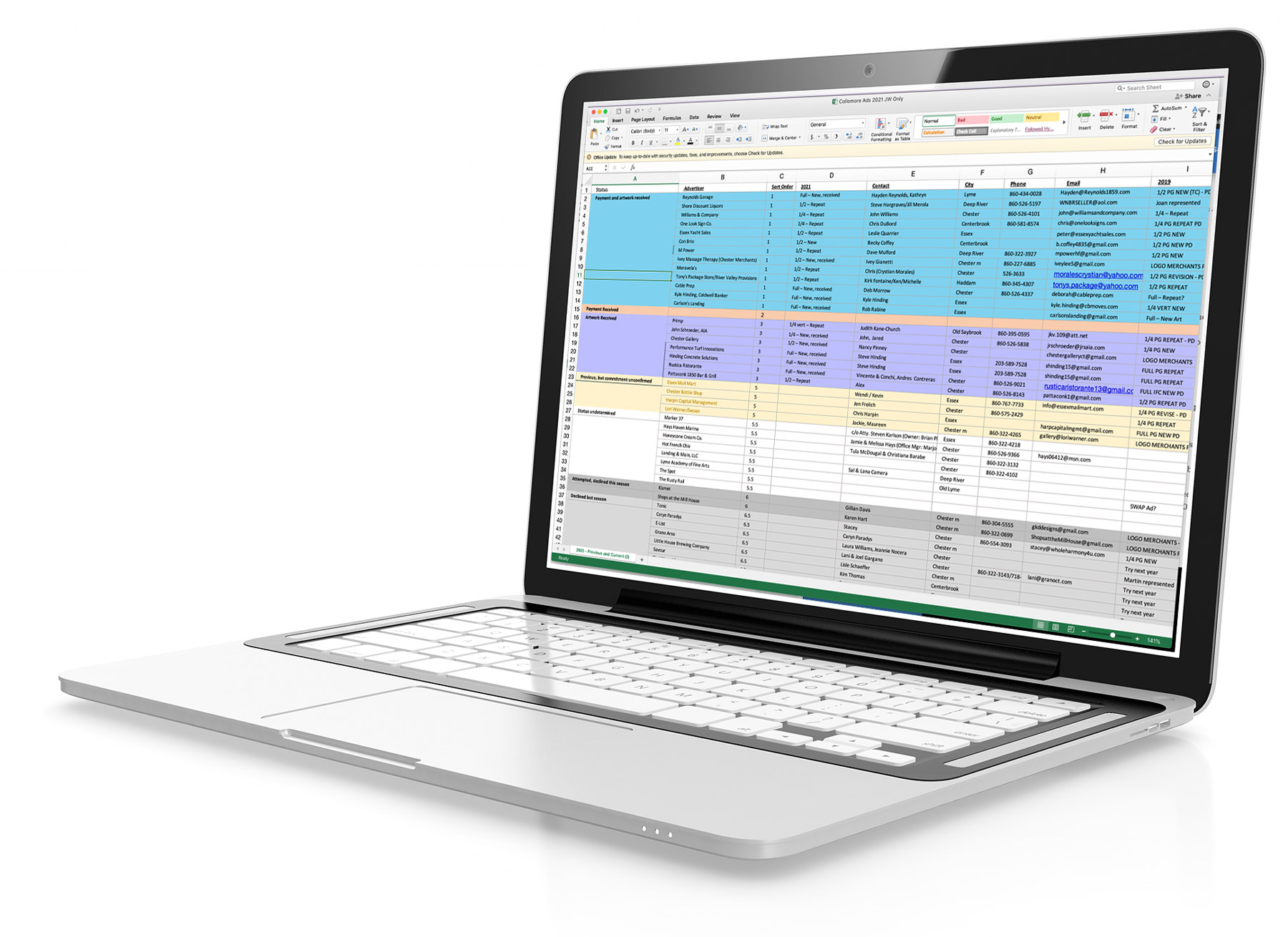
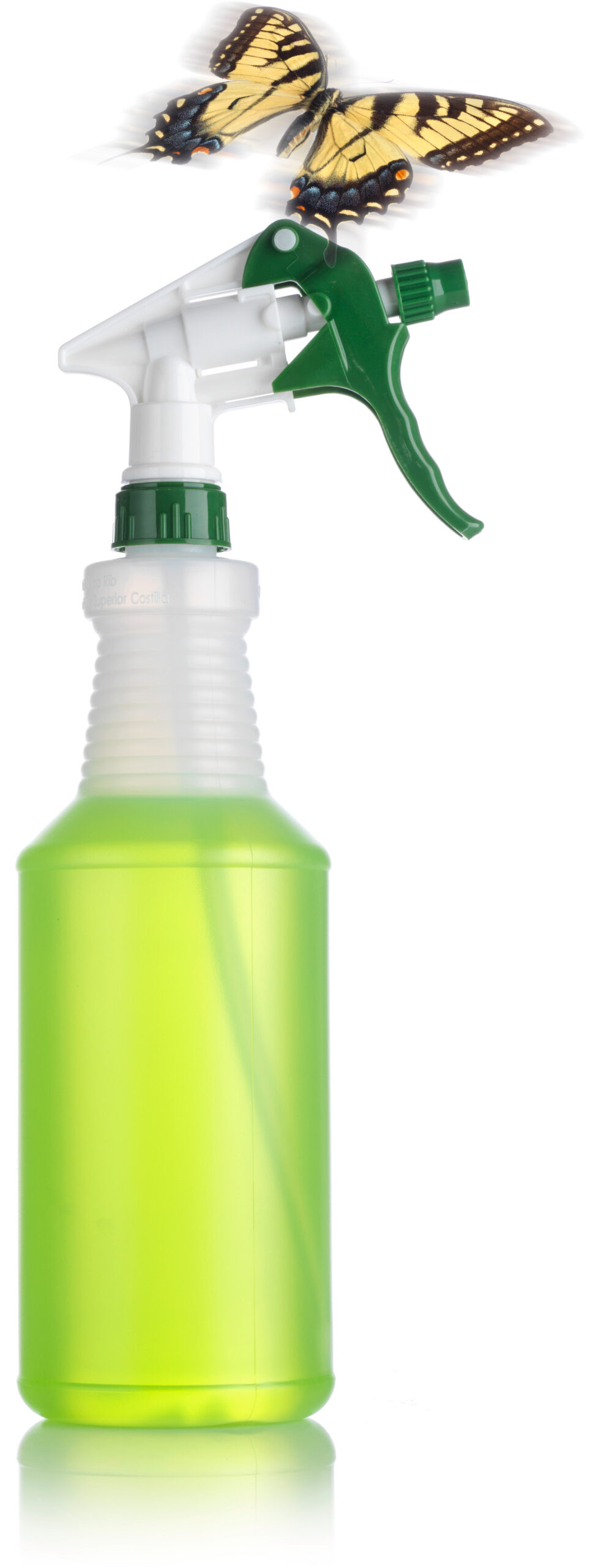

Green Cleaning
Delta Building Services is cognizant of the changing world and the importance of protecting the environment. Realizing this goal has affected Delta’s approach to cleaning and to the type of products that are used. Since 2006, Delta has been performing green cleaning. It has discovered that it is not only highly effective for environmental reasons, but for health and productivity as well.
Green cleaning became popular because of its reduction in environmental damage. Additional research demonstrates its positive impact due to its lower toxicity levels for humans and animals. Green cleaning products do not require as much energy to create, transport and store. Delta uses these products to benefit both the cleaners and the building occupants.
Delta has also become an active participant in the LEED Green certification program operated by the U.S. Green Building Council. The LEED program for Existing Buildings requires participation by Janitorial Service companies like ours to cooperate if owners and managers are to achieve “points” and ultimately savings. Delta’s Optional Day Cleaning program can help to achieve points in two categories. First in the Energy and Atmosphere category, Delta’s day program means that we will not be the reason lights are kept on after hours. Second, and more importantly, in the Indoor Environmental Quality Category, Delta’s Day Cleaning Program follows the intent and the requirements set forth by the USGBC. Where clients allow us to, we provide a staffing plan, training, chemical guidelines, sustainable cleaning materials and equipment required by the USGBC’s High Performance Cleaning Program.
Delta uses Rochester Midland Corporation “Enviro Care” cleaning products. RMC was the first company in the world to receive Green Seal Certification for institutional and industrial cleaning. Their products are Non-toxic, non-corrosive, non-combustible, non-reactive and have no hazardous ingredients, glycol ethers, petroleum distillates, suspected carcinogens, or ozone-depleting compounds. The SNAP high-tech dispensing unit is safe, accurate and easy to use.
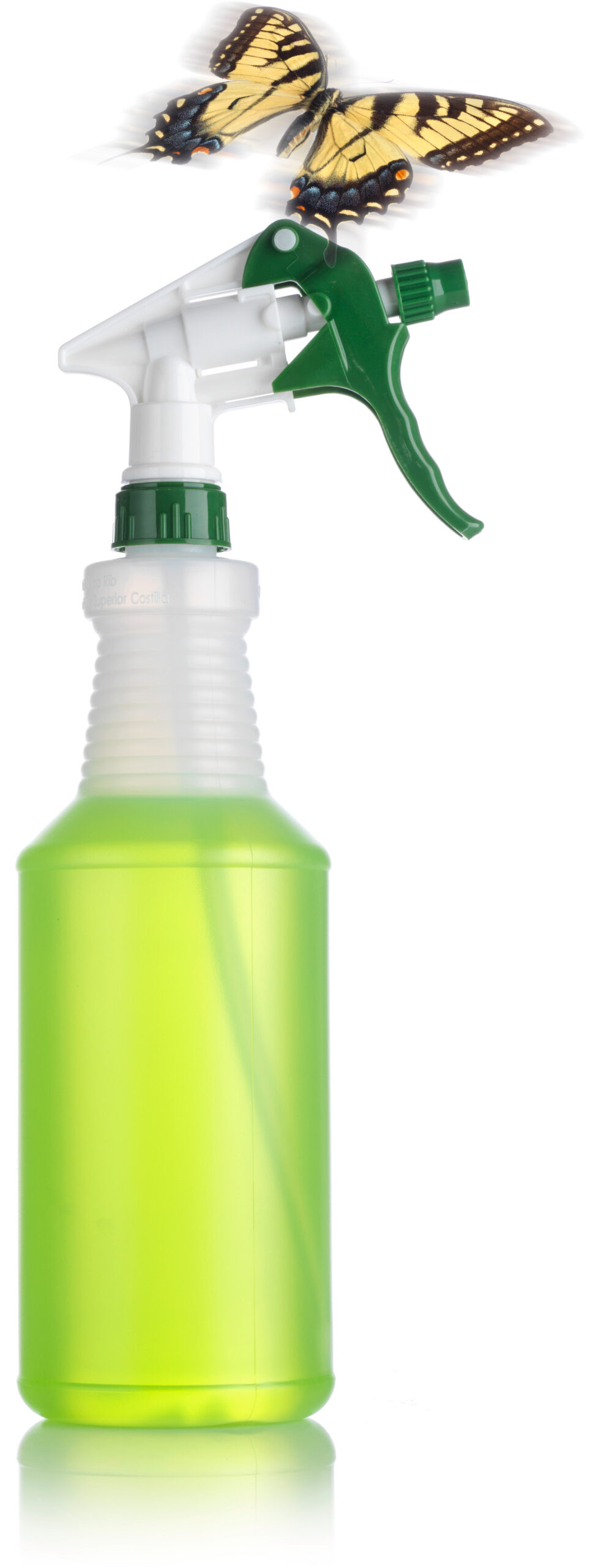

Certifications
Victory innovations: Certification: Infection Prevention Certification course instructing the use of electrostatic spraying equipment, disinfection techniques and training relating to fighting COVID-19.
Building Service Contractors Association International: Certified: COVID-19 Disinfection and Safety Course.
ISSA – GBAC: Certified: “GBAC Fundamentals Online Course: Cleaning & Disinfection Principles” a training/certification course relating to the identification, evaluation, reduction and elimination of biological threats.
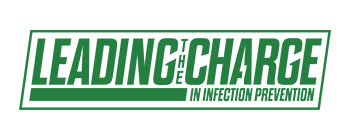
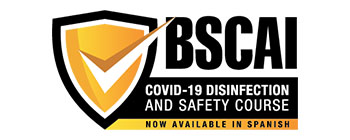
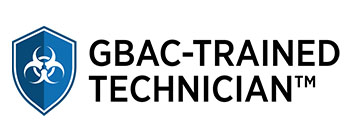

Affiliations
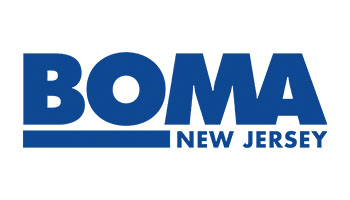
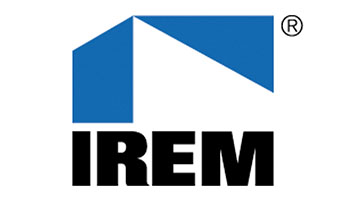
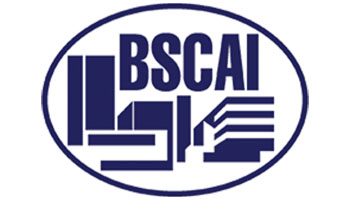
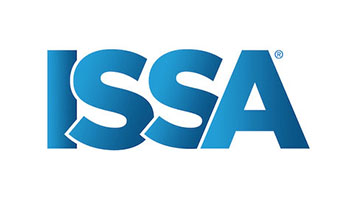
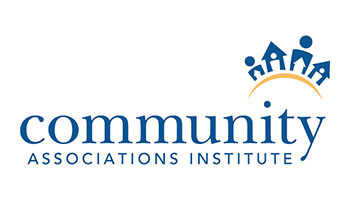
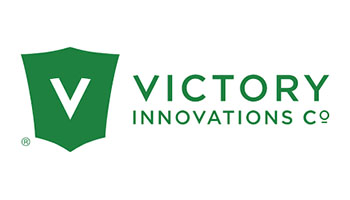